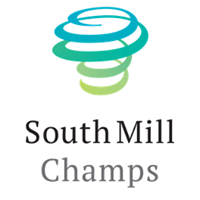
1932 – THE BEGINNING
South Mill’s roots began 4 generations ago in 1932 when John Pia, an Italian immigrant, began operating a small mushroom farm in southeastern Chester County, Pennsylvania.
1950 – PRODUCING SUBSTRATE
The focus of the business changes from mushroom growing to the production and sale of mushroom growing substrate to local mushroom growers
1982 – THE NEXT BIG STEP
The Pia family, through its marketing division of South Mill Mushroom Sales, purchased their Kennett Square, Pennsylvania mushroom-growing operation from the Clorox Corporation. Clorox operated the facility under the “Grocery Store Products” label, selling predominantly to the cannery markets. South Mill converted the production of this facility to the fresh market, which was just beginning to develop in the United States.
1984 – A NEW GROWING DIVISION PURCHASED
A large mushroom farm in Landenberg, Pennsylvania of nearly 30 growing rooms is purchased, thereby adding to South Mill’s expanding mushroom growing capacity.
1984 – VACUUM COOLING
Vacuum cooling, a technology only recently available at the time, is implemented via the purchase of a 15,000 pounds capacity vacuum cooler, providing the ability to properly cool mushrooms in just 20 minutes versus the 24 hours it previously took in typical cold storage coolers.
1986 – DIRECT HARVESTING
South Mill converts from the prior standard harvesting practice of dumping mushrooms into the final sales container at the packing area to a practice of harvesting directly into the final sales container at the farm level, thereby reducing bruising and improving quality and shelf-life.
1994 – SOUTH MILL DISTRIBUTION IS BORN
South Mill Distribution, the company’s concept of “bringing the farm to market” by establishing regional distribution centers throughout the United States near major metropolitan cities, is launched in Dallas Texas. These distribution centers receive bulk mushrooms and other produce items shipped from Kennett Square.
1996 – NEW COMPOSTING TECHNOLOGY!
South Mill begins testing a new technology to produce mushroom growing substrate indoors in specially designed fermentation bunkers or “tunnels”. This process will supply South Mill with the highest quality, most efficiently produced mushroom growing substrate, while nearly completely eliminating any negative impact on the neighboring area or the environment.
1996 – SOUTH MILL DISTRIBUTION EXPANDS, WITH FACILITY #2 & #3
A new distribution center opens in Houston, Texas based upon the success of the “farm to market” concept initiated in Dallas. Additionally, a transfer station is established in Statesville, North Carolina to accommodate freight transfers of northbound freight or southbound mushrooms, and produce items.
1998 – SOUTH MILL DISTR
IBUTION ADDS FACILITY #4
New Orleans, Louisiana opens! Our “farm-to-market” concept expands into the Gulf Coast states, capitalizing on what has become a well-established transportation network. The exceptional humidity issues associated with this region accentuate the benefits of our “farm-to-market” concept. This allows South Mill to service these distance markets from over 1,000 miles away in competition with local mushroom providers.
2000 – TWELVE FERMENTATION TUNNELS START-UP
Twelve fully enclosed Phase I mushroom substrate fermentation tunnels – the first of their kind in North America – go live! The beneficial results of this new technology are immediately evident in South Mill’s productivity, and the project is applauded by the local community and government.
2000 – SOUTH MILL DISTRIBUTION TAKES ON THE SOUTHEAST
Atlanta, Georgia opens! Filling a geographic void in the southeastern region, the upscale metropolitan market of Atlanta was chosen to establish our fifth distribution center. Acting as a hub for the southeastern routes, our distribution services utilize Atlanta as a jumping-off point for the Gulf Coast distribution region, as well as for Florida-bound freight and mushroom shipments. The company has multiple trucks per day connecting through the city of Atlanta.
2002 – SIX PASTEURIZATION TUNNELS ROLL-OUT!
While the process of indoor pasteurization (Phase II) has been utilized to a small degree in the US, South Mill’s new facility is the first to incorporate “walking floor” technology in the material-handling process.
2003 – PHASE I EXPANSION
Six additional Phase I tunnels are added at the composting facility increasing output by 50%.
2004 – PRODUCT LINES ADDED
Product line offerings are expanded to include many fruits and vegetables complementary to the needs of our mushroom customers.
2005 – MODERN LOGISTICS TECHNOLOGY
South Mill was one of the first mushroom farms in the country to install modern logistics technology in its over-the-road refrigerated transportation fleet. This allows “in-transit” data to be communicated in real-time. Important delivery data including, change of schedule, change of delivery locations and estimated times of arrival (ETA) can be communicated to the customer. With one of the largest geographic distribution footprints of any mushroom farm in North America, the goal of efficiently communicating on a 24/7 basis, with trucks travelling thru most every major city east of the Rockies, and in Canada, underscores the company’s commitment to customer service.
2006 – SOUTH MILL SECURES NATIONAL BRAND MARKETING RIGHTS
South Mill (one of only two suppliers of white mushrooms nationwide) secures rights, as a sub-licensee, to market the “Dole” brand on a national basis for all fresh mushroom products. The Dole label is one of the most well-known and respected produce labels in the world.
2007 – SEVEN ADDITIONAL PASTEURIZATION TUNNELS ONLINE
With the construction of seven additional Phase II tunnels, South Mill significantly increases its capacity to produce Phase II substrate to be used internally as well as for sale to local mushroom farmers, thereby creating a new and diversified business unit for the company.
2008 – FOOD SAFETY, OUR PROUDEST ACHIEVEMENT
South Mill becomes the first, and only, mushroom farm in the United States to pass the new, higher standards of food safety as defined by the recently published USDA MGAP audit. No higher commitment to food safety can be exemplified than the effort South Mill made to set a leadership tone for the mushroom industry by volunteering to be the first mushroom farm in the country to undergo this world class standard.
2009 – SOUTH MILL ASSUMES MANFREDINI ENTERPRISES!!
South Mill assumed the business of Manfredini Enterprises, a local mushroom distributor with operations in North Lima, Ohio and Louisville, Kentucky. Benefits included a supply base of quality mushrooms and access to the New England and Eastern Midwest marketing regions.
2009 – COLD STORAGE ADDED
South Mill adds a refrigerated and frozen storage facility at its headquarters with a capacity of 2,000 pallets offering our customer yet another beneficial service.
2010 – IQF BEGINS
South Mill begins operation of its new Individually Quick Frozen (IQF) process with a capacity of 20 million pounds annually.
2010 – SOUTH MILL EXPANDS ITS GROWING
South Mill purchases a large mushroom farm in West Grove, Pennsylvania with 36 growing rooms, increasing our overall growing capacity by 20%.
2011 – PORTABELLA PRODUCTION BEGINS!
In late 2011, the company began the production of portabella and cremini mushrooms from a new location near our headquarters in Kennett Square, PA. This expansion has resulted in the internal production of 75% of the company’s needs for the brown varieties that are becoming so popular. Due to the success of this new expansion, the company is considering a phase 2 expansion to add another 25% to its production of brown mushrooms.
2012 – STRAW BALING BEGINS
South Mill begins baling wheat straw in North Carolina to supplement existing sources and to help secure a sustainable supply of this critical raw material. Wheat straw is the largest component in our substrate formulation.
2012 – NEW HOME FOR OUR HOUSTON DIVISION!
In early 2011, our Houston division purchased a warehouse near the produce center of the city. Extensive renovations of this 25,000 sq. foot facility commenced in the fall of 2011. Completion and occupancy took place in Q1 2012. Multiple temperature zones, repacking facilities, and state-of-the-art processing capabilities will provide our Houston division with 50% more storage and operating capacity.
2015 – GOING GREEN!
South Mill receives its organic handler certification for our IQF facility. Our upcoming organic growing and fresh handling certification will be obtained in early 2016 allowing South Mill to fill the needs of the expanding organic market.
Location: United States, Pennsylvania, Kennett Township
Employees: 501-1000
Phone: +1 610-444-4800
Founded date: 1962
Investors 1
Date | Name | Website |
- | Eos Partne... | eospartner... |
Mentions in press and media 3
Date | Title | Description | Source |
29.02.2024 | South Mill Champs and Grupo APAL Form Strategic Joint Ventur... | KENNETT SQUARE, Pa., Feb. 29, 2024 /PRNewswire/ -- South Mill Champs, a leading North American growe... | en.prnasia... |
05.01.2021 | South Mill Champs Expands Mushrooms Processing Capabilities ... | prnewswire... | |
02.11.2020 | South Mill Champs Expands its Distribution Network with New ... | prnewswire... |