The Art of Precision: Avoiding Common Mistakes in Flat Tensile Sample Preparation
December 18, 2024, 5:29 pm
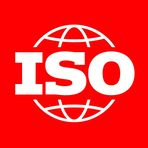
Location: Switzerland, Geneva, Vernier
Employees: 201-500
Founded date: 1947
In the world of materials testing, precision is king. Flat tensile sample preparation is the foundation upon which accurate testing results are built. Think of it as the blueprint for a skyscraper. If the blueprint is flawed, the building will crumble. This article delves into the common pitfalls in sample preparation and offers strategies to sidestep these errors, ensuring that the testing process is as reliable as a well-oiled machine.
Flat tensile testing is crucial for understanding a material's mechanical properties. Tensile strength, yield strength, and elongation are just a few metrics that define how a material will perform under stress. However, even minor missteps in sample preparation can lead to significant discrepancies in results. This not only jeopardizes product quality but can also lead to costly retests and potential compliance issues with industry standards.
One of the most critical aspects of flat tensile sample preparation is achieving precise dimensions. Imagine trying to fit a square peg into a round hole. If the dimensions are off, the stress distribution during testing will be skewed, leading to unreliable measurements.
Common mistakes in this area often stem from outdated equipment or operator errors. A specimen that is too thick or too thin can create stress concentrations that distort tensile strength readings. The consequences are dire: inconsistent specimen sizes lead to skewed data, making it nearly impossible to compare results across tests or verify compliance with standards like ASTM E8 or ISO 6892.
To combat these issues, precision equipment is essential. CNC milling machines can provide the accuracy needed for tensile specimen preparation. Regular calibration of these machines is also crucial. It’s like tuning a musical instrument; if it’s out of tune, the performance will suffer. Following standardized dimensions and using templates can further ensure that specimens meet required specifications.
The surface finish of flat tensile samples is another critical factor that can impact testing results. A rough surface can introduce stress concentrators, weakening the sample and leading to premature failure. Picture a bumpy road; it’s bound to cause a rough ride.
Poor surface finishes often arise from using inappropriate finishing tools or skipping essential polishing steps. Jagged edges can act as points of weakness, compromising the integrity of the sample. The result? Inaccurate measurements of tensile strength and elongation.
To avoid these pitfalls, employing proper surface finishing techniques is vital. Grinding or polishing methods can achieve a smooth, uniform finish, ensuring consistent stress distribution during testing. Additionally, using deburring tools to remove sharp edges can significantly reduce stress concentration points. A final inspection under magnification can catch any imperfections that might affect the test.
Alignment and gripping of the sample in the testing machine are pivotal for accurate results. Misalignment can lead to uneven stress distribution, akin to trying to balance a tightrope while wearing shoes two sizes too big.
Common mistakes include improper gripping or misalignment during testing. This can result in off-axis loading, invalidating the test and necessitating retesting. The wear and tear on testing equipment can also increase, leading to further costs.
To ensure proper alignment, samples should be centered and parallel to the loading axis. Using grips designed for the specific material and geometry can prevent slippage or damage. Regular maintenance of grips is also essential to guarantee consistent clamping force.
Achieving accuracy in flat tensile sample preparation is not just about avoiding mistakes; it’s about cultivating a culture of precision. Organizations must invest in high-quality tools and adhere to industry standards. Regular equipment maintenance and personnel training are key components of this culture.
By understanding the importance of proper sample preparation and implementing best practices, organizations can achieve reliable and repeatable tensile testing results. This not only supports product quality and compliance but also reinforces trust in the testing process, contributing to overall operational success.
In conclusion, the art of flat tensile sample preparation is a delicate dance of precision and care. Each step, from dimensional accuracy to surface finish and alignment, plays a crucial role in the final outcome. By avoiding common mistakes and embracing best practices, professionals can ensure that their tensile testing processes yield consistent, reliable, and meaningful results. The stakes are high, but with diligence and attention to detail, success is within reach.
Flat tensile testing is crucial for understanding a material's mechanical properties. Tensile strength, yield strength, and elongation are just a few metrics that define how a material will perform under stress. However, even minor missteps in sample preparation can lead to significant discrepancies in results. This not only jeopardizes product quality but can also lead to costly retests and potential compliance issues with industry standards.
Dimensional Inaccuracies: The Silent Saboteur
One of the most critical aspects of flat tensile sample preparation is achieving precise dimensions. Imagine trying to fit a square peg into a round hole. If the dimensions are off, the stress distribution during testing will be skewed, leading to unreliable measurements.
Common mistakes in this area often stem from outdated equipment or operator errors. A specimen that is too thick or too thin can create stress concentrations that distort tensile strength readings. The consequences are dire: inconsistent specimen sizes lead to skewed data, making it nearly impossible to compare results across tests or verify compliance with standards like ASTM E8 or ISO 6892.
To combat these issues, precision equipment is essential. CNC milling machines can provide the accuracy needed for tensile specimen preparation. Regular calibration of these machines is also crucial. It’s like tuning a musical instrument; if it’s out of tune, the performance will suffer. Following standardized dimensions and using templates can further ensure that specimens meet required specifications.
Surface Finish: The Unsung Hero
The surface finish of flat tensile samples is another critical factor that can impact testing results. A rough surface can introduce stress concentrators, weakening the sample and leading to premature failure. Picture a bumpy road; it’s bound to cause a rough ride.
Poor surface finishes often arise from using inappropriate finishing tools or skipping essential polishing steps. Jagged edges can act as points of weakness, compromising the integrity of the sample. The result? Inaccurate measurements of tensile strength and elongation.
To avoid these pitfalls, employing proper surface finishing techniques is vital. Grinding or polishing methods can achieve a smooth, uniform finish, ensuring consistent stress distribution during testing. Additionally, using deburring tools to remove sharp edges can significantly reduce stress concentration points. A final inspection under magnification can catch any imperfections that might affect the test.
Alignment and Gripping: The Balancing Act
Alignment and gripping of the sample in the testing machine are pivotal for accurate results. Misalignment can lead to uneven stress distribution, akin to trying to balance a tightrope while wearing shoes two sizes too big.
Common mistakes include improper gripping or misalignment during testing. This can result in off-axis loading, invalidating the test and necessitating retesting. The wear and tear on testing equipment can also increase, leading to further costs.
To ensure proper alignment, samples should be centered and parallel to the loading axis. Using grips designed for the specific material and geometry can prevent slippage or damage. Regular maintenance of grips is also essential to guarantee consistent clamping force.
The Path to Precision
Achieving accuracy in flat tensile sample preparation is not just about avoiding mistakes; it’s about cultivating a culture of precision. Organizations must invest in high-quality tools and adhere to industry standards. Regular equipment maintenance and personnel training are key components of this culture.
By understanding the importance of proper sample preparation and implementing best practices, organizations can achieve reliable and repeatable tensile testing results. This not only supports product quality and compliance but also reinforces trust in the testing process, contributing to overall operational success.
In conclusion, the art of flat tensile sample preparation is a delicate dance of precision and care. Each step, from dimensional accuracy to surface finish and alignment, plays a crucial role in the final outcome. By avoiding common mistakes and embracing best practices, professionals can ensure that their tensile testing processes yield consistent, reliable, and meaningful results. The stakes are high, but with diligence and attention to detail, success is within reach.