Scania's Bold Leap into Sustainable Manufacturing and Autonomous Mining
September 30, 2024, 5:08 pm
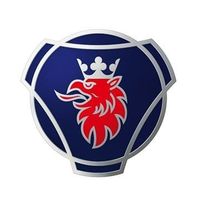
Location: Sweden, Södertälje
Employees: 10001+
Founded date: 1891
Total raised: $190.6M
In a world increasingly focused on sustainability, Scania is leading the charge. The Swedish truck manufacturer has made headlines with two groundbreaking initiatives: the integration of remanufactured components into its assembly line and a partnership with Fortescue to develop autonomous mining road trains. These projects not only showcase innovation but also highlight a shift towards a more sustainable future in the transport and mining industries.
Scania's recent achievement in remanufacturing is a game-changer. The company has become the first truck manufacturer to incorporate reused components directly into its main assembly line. This milestone was made possible through the iReGear project, a collaboration with KTH Royal Institute of Technology and Scandinavian Transmission Service AB, backed by Sweden's innovation agency, Vinnova. The remanufactured gearbox produced through this initiative consumed 50% less material and emitted 45% fewer carbon emissions compared to new gearboxes.
Imagine a world where old parts are not discarded but reborn. This is the essence of remanufacturing. It’s like turning yesterday’s news into today’s headlines. Scania’s remanufactured gearbox underwent the same rigorous testing as new components, proving that quality does not have to be sacrificed for sustainability. This process is a vital step towards a circular economy, where resources are reused rather than wasted.
The automotive industry has long viewed remanufacturing as a promising strategy for reducing environmental impact. Yet, it has largely been confined to aftermarket parts. Scania’s initiative challenges this norm. By integrating remanufactured components into new vehicle production, Scania sets a precedent for the industry. This shift could pave the way for broader adoption of sustainable practices in manufacturing.
The potential of remanufacturing is immense. It addresses resource scarcity and reduces waste. However, for it to become mainstream, manufacturers must embrace this model. Scania’s pioneering efforts could inspire others to follow suit, transforming the landscape of vehicle production.
Meanwhile, Scania is not stopping at remanufacturing. The company is also venturing into the realm of autonomous vehicles. In partnership with Fortescue, an Australian mining giant, Scania is developing an autonomous road train solution. This collaboration aims to revolutionize the mining industry by reducing its environmental footprint while enhancing efficiency.
The mining sector is notorious for its resource-intensive operations. However, with Scania’s expertise in truck automation and Fortescue’s knowledge of autonomous haulage, this project promises to change the game. The autonomous road train will be tested in the challenging conditions of Fortescue’s iron ore operations in Queensland. This partnership exemplifies how technology can drive sustainability in even the most demanding environments.
Picture a convoy of trucks, seamlessly navigating the rugged terrain without human intervention. This is the future Scania and Fortescue are working towards. The autonomous solution will integrate with Fortescue’s Fleet Management System, optimizing fleet utilization and minimizing fuel consumption. This synergy aims to maximize productivity while significantly reducing carbon emissions.
Safety and efficiency are at the forefront of this initiative. The harsh conditions of mining require robust solutions. Scania’s technology, combined with Fortescue’s operational expertise, aims to create a safer and more efficient mining process. This collaboration reflects a shared commitment to sustainability and operational excellence.
Scania’s dual focus on remanufacturing and autonomous technology illustrates a broader trend in the transport and mining industries. Companies are increasingly recognizing the importance of sustainability. The pressure to reduce carbon footprints is mounting, and innovative solutions are essential.
The implications of Scania’s initiatives extend beyond their immediate impact. They signal a shift in how industries approach manufacturing and resource management. As companies adopt more sustainable practices, the potential for positive change grows. Scania’s efforts could inspire a ripple effect, encouraging others to rethink their operations.
In conclusion, Scania is not just a truck manufacturer; it is a pioneer in sustainable innovation. The integration of remanufactured components into production lines and the development of autonomous mining solutions are significant steps towards a greener future. These initiatives demonstrate that sustainability and efficiency can go hand in hand. As Scania leads the way, the hope is that others will follow, creating a more sustainable transport and mining industry for generations to come. The road ahead is challenging, but with bold steps like these, the journey towards sustainability is well underway.
Scania's recent achievement in remanufacturing is a game-changer. The company has become the first truck manufacturer to incorporate reused components directly into its main assembly line. This milestone was made possible through the iReGear project, a collaboration with KTH Royal Institute of Technology and Scandinavian Transmission Service AB, backed by Sweden's innovation agency, Vinnova. The remanufactured gearbox produced through this initiative consumed 50% less material and emitted 45% fewer carbon emissions compared to new gearboxes.
Imagine a world where old parts are not discarded but reborn. This is the essence of remanufacturing. It’s like turning yesterday’s news into today’s headlines. Scania’s remanufactured gearbox underwent the same rigorous testing as new components, proving that quality does not have to be sacrificed for sustainability. This process is a vital step towards a circular economy, where resources are reused rather than wasted.
The automotive industry has long viewed remanufacturing as a promising strategy for reducing environmental impact. Yet, it has largely been confined to aftermarket parts. Scania’s initiative challenges this norm. By integrating remanufactured components into new vehicle production, Scania sets a precedent for the industry. This shift could pave the way for broader adoption of sustainable practices in manufacturing.
The potential of remanufacturing is immense. It addresses resource scarcity and reduces waste. However, for it to become mainstream, manufacturers must embrace this model. Scania’s pioneering efforts could inspire others to follow suit, transforming the landscape of vehicle production.
Meanwhile, Scania is not stopping at remanufacturing. The company is also venturing into the realm of autonomous vehicles. In partnership with Fortescue, an Australian mining giant, Scania is developing an autonomous road train solution. This collaboration aims to revolutionize the mining industry by reducing its environmental footprint while enhancing efficiency.
The mining sector is notorious for its resource-intensive operations. However, with Scania’s expertise in truck automation and Fortescue’s knowledge of autonomous haulage, this project promises to change the game. The autonomous road train will be tested in the challenging conditions of Fortescue’s iron ore operations in Queensland. This partnership exemplifies how technology can drive sustainability in even the most demanding environments.
Picture a convoy of trucks, seamlessly navigating the rugged terrain without human intervention. This is the future Scania and Fortescue are working towards. The autonomous solution will integrate with Fortescue’s Fleet Management System, optimizing fleet utilization and minimizing fuel consumption. This synergy aims to maximize productivity while significantly reducing carbon emissions.
Safety and efficiency are at the forefront of this initiative. The harsh conditions of mining require robust solutions. Scania’s technology, combined with Fortescue’s operational expertise, aims to create a safer and more efficient mining process. This collaboration reflects a shared commitment to sustainability and operational excellence.
Scania’s dual focus on remanufacturing and autonomous technology illustrates a broader trend in the transport and mining industries. Companies are increasingly recognizing the importance of sustainability. The pressure to reduce carbon footprints is mounting, and innovative solutions are essential.
The implications of Scania’s initiatives extend beyond their immediate impact. They signal a shift in how industries approach manufacturing and resource management. As companies adopt more sustainable practices, the potential for positive change grows. Scania’s efforts could inspire a ripple effect, encouraging others to rethink their operations.
In conclusion, Scania is not just a truck manufacturer; it is a pioneer in sustainable innovation. The integration of remanufactured components into production lines and the development of autonomous mining solutions are significant steps towards a greener future. These initiatives demonstrate that sustainability and efficiency can go hand in hand. As Scania leads the way, the hope is that others will follow, creating a more sustainable transport and mining industry for generations to come. The road ahead is challenging, but with bold steps like these, the journey towards sustainability is well underway.