LG Innotek's Digital Twin Revolution: A Leap into Meta-Manufacturing
August 23, 2024, 11:44 pm
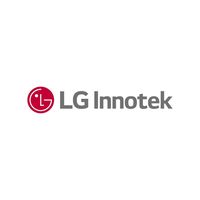
Location: Poland, Lower Silesian Voivodeship, Kobierzyce
Employees: 5001-10000
Founded date: 1970
In the fast-paced world of technology, LG Innotek is making waves. The South Korean company is on a mission to redefine manufacturing through its partnership with Ansys, a leader in engineering simulation. This collaboration aims to harness the power of Digital Twin technology, a game-changer in the manufacturing landscape.
Digital Twin technology is like a crystal ball for manufacturers. It creates a virtual replica of physical objects, allowing companies to simulate real-world scenarios. This innovation can predict outcomes, streamline processes, and ultimately save time and money. LG Innotek is diving headfirst into this technology, aiming to transform its operations and enhance competitiveness.
The partnership with Ansys is a strategic move. Ansys brings expertise in 3D modeling, artificial intelligence (AI), and machine learning (ML). Together, they are crafting a sophisticated Digital Twin environment. This collaboration is not just about theory; it has already yielded impressive results. Initial trials have shown that LG Innotek can reduce development time by a staggering 99%.
Imagine cutting down the time it takes to verify designs from 11 days to just 3.6 hours. That’s the power of virtual simulation. By optimizing the design of package substrates for semiconductors, LG Innotek is setting a new standard in efficiency. This technology minimizes the need for extensive physical testing, which can be both time-consuming and costly.
But the benefits don’t stop there. LG Innotek is expanding the application of Digital Twin technology beyond R&D. The company is now applying it to the production of Flip-Chip Ball-Grid Array (FC-BGA) components. In the past, identifying optimal production conditions required hundreds of tests. Now, with the help of 3D modeling, LG Innotek can replicate the entire production process in a virtual space. This not only saves time but also significantly reduces costs.
The virtual environment allows for meticulous optimization. It visualizes potential issues that could arise during production, such as the flow of liquids and heat. This level of detail is impossible to achieve through traditional methods. By fine-tuning these conditions, LG Innotek has halved the ramp-up period for production. This means faster time-to-market and increased competitiveness.
In the realm of electric vehicles, LG Innotek is also making strides. The company has applied Digital Twin technology to the soldering process, a critical step in ensuring the reliability of electronic vehicle components. By simulating this process, LG Innotek can predict when solder might crack. This foresight allows for adjustments that can increase productivity by 40%.
The vision for LG Innotek is clear: to become a meta-manufacturing company. This concept involves linking virtual simulations directly to physical production facilities. The goal is to create a seamless flow from design to production, where data generated in the virtual space informs real-world manufacturing processes.
As LG Innotek expands its use of Digital Twin technology, it plans to involve customers and partners across the entire value chain. This collaborative approach will enable stakeholders to work together on product design and simulate production efficiency. Real-time data sharing will enhance quality control and streamline development processes.
AI will play a crucial role in this transformation. By integrating AI into the virtual design and quality verification processes, LG Innotek aims to boost simulation speed and accuracy. The AI will learn from the data collected, providing optimal solutions and supporting engineers in decision-making. This synergy between virtualization and AI is expected to multiply productivity gains.
The implications of this technological leap are profound. LG Innotek is not just improving its own processes; it is setting a benchmark for the industry. The ability to rapidly prototype, test, and produce products will redefine manufacturing standards. Companies that embrace Digital Twin technology will find themselves at a significant advantage.
In conclusion, LG Innotek is leading the charge into a new era of manufacturing. With its partnership with Ansys and the implementation of Digital Twin technology, the company is poised to revolutionize how products are developed and produced. The future of manufacturing is here, and it is digital. As LG Innotek continues to innovate, it will undoubtedly inspire others to follow suit. The road ahead is bright, and the possibilities are endless.
Digital Twin technology is like a crystal ball for manufacturers. It creates a virtual replica of physical objects, allowing companies to simulate real-world scenarios. This innovation can predict outcomes, streamline processes, and ultimately save time and money. LG Innotek is diving headfirst into this technology, aiming to transform its operations and enhance competitiveness.
The partnership with Ansys is a strategic move. Ansys brings expertise in 3D modeling, artificial intelligence (AI), and machine learning (ML). Together, they are crafting a sophisticated Digital Twin environment. This collaboration is not just about theory; it has already yielded impressive results. Initial trials have shown that LG Innotek can reduce development time by a staggering 99%.
Imagine cutting down the time it takes to verify designs from 11 days to just 3.6 hours. That’s the power of virtual simulation. By optimizing the design of package substrates for semiconductors, LG Innotek is setting a new standard in efficiency. This technology minimizes the need for extensive physical testing, which can be both time-consuming and costly.
But the benefits don’t stop there. LG Innotek is expanding the application of Digital Twin technology beyond R&D. The company is now applying it to the production of Flip-Chip Ball-Grid Array (FC-BGA) components. In the past, identifying optimal production conditions required hundreds of tests. Now, with the help of 3D modeling, LG Innotek can replicate the entire production process in a virtual space. This not only saves time but also significantly reduces costs.
The virtual environment allows for meticulous optimization. It visualizes potential issues that could arise during production, such as the flow of liquids and heat. This level of detail is impossible to achieve through traditional methods. By fine-tuning these conditions, LG Innotek has halved the ramp-up period for production. This means faster time-to-market and increased competitiveness.
In the realm of electric vehicles, LG Innotek is also making strides. The company has applied Digital Twin technology to the soldering process, a critical step in ensuring the reliability of electronic vehicle components. By simulating this process, LG Innotek can predict when solder might crack. This foresight allows for adjustments that can increase productivity by 40%.
The vision for LG Innotek is clear: to become a meta-manufacturing company. This concept involves linking virtual simulations directly to physical production facilities. The goal is to create a seamless flow from design to production, where data generated in the virtual space informs real-world manufacturing processes.
As LG Innotek expands its use of Digital Twin technology, it plans to involve customers and partners across the entire value chain. This collaborative approach will enable stakeholders to work together on product design and simulate production efficiency. Real-time data sharing will enhance quality control and streamline development processes.
AI will play a crucial role in this transformation. By integrating AI into the virtual design and quality verification processes, LG Innotek aims to boost simulation speed and accuracy. The AI will learn from the data collected, providing optimal solutions and supporting engineers in decision-making. This synergy between virtualization and AI is expected to multiply productivity gains.
The implications of this technological leap are profound. LG Innotek is not just improving its own processes; it is setting a benchmark for the industry. The ability to rapidly prototype, test, and produce products will redefine manufacturing standards. Companies that embrace Digital Twin technology will find themselves at a significant advantage.
In conclusion, LG Innotek is leading the charge into a new era of manufacturing. With its partnership with Ansys and the implementation of Digital Twin technology, the company is poised to revolutionize how products are developed and produced. The future of manufacturing is here, and it is digital. As LG Innotek continues to innovate, it will undoubtedly inspire others to follow suit. The road ahead is bright, and the possibilities are endless.